焊接件是各类工程机械设备结构中的重要组成部分。在施工作业过程中,焊接件开裂是设备常见故障之一。焊接开裂时,会影响设备正常运行,甚至造成无法作业,导致停工。对工程机械常见焊接件开裂与修复技术的研究,是设计、工艺与维修人员密切关注的课题。 随着工程机械焊接结构趋向于高参数、大型化、耐磨、重载、轻量化的方向发展,焊接构件制造也不断应用新材料、新工艺、新技术。焊接构件不仅要满足产品设计性能、参数要求,还要求焊接接头具备更高的可靠性,同样对焊接件开裂预防与修复技术也要求更加严格。
1 焊接开裂的基本原因 企业在产品结构件设计、加工、检验等过程建立了有效的质量控制体系,力求提高焊接接头性能,达到预防、消除焊接缺欠,保证焊缝可靠性的目标。但是,焊接由于其自身的特点而被视为“特殊过程”。 这是因为焊接作为一种热加工技术,其随后的检验根本无法充分验证其加工结果,不能完全控制与了解焊接接头性能是否达到了预期的要求。事实上,所有的焊接产品都是带着这种未知的“问号”进入用户的手中运行和使用。 在设备作业运行中,当构件受到冲击、拉压、扭转、弯曲载荷与过载、震动、环境温度变化等复杂工况时,避免不了形成裂纹,裂纹逐渐扩展导致焊接开裂直至构件断开失效。所以这种“特殊过程”的缘故,造成焊接接头性能的不稳定性,导致接头强度下降,是焊接开裂的基本原因。
2 焊接件类别与焊接开裂分析 工程机械产品品种繁多、焊接件几何形状复杂,尺寸、重量相差悬殊,工序长短和复杂程度也各不相同。大都是采用焊条电弧焊、气体保护焊、埋弧焊等焊接工艺方法。 对工程机械产品焊接件分类并进行开裂分析: 2.1按焊接件结构特点,见表一。
 表一 2.2按焊接件功能,见表二。
 表二 2.3按钢材强度级别,见表三。
 表三 通过以上对焊接件分类与焊接开裂的分析可以看出,焊接件开裂主要集中在工作装置类构件。这是因为此类焊接件不仅结构复杂、承受大的工作载荷,抗变形能力差,而且采用的钢材品种多、强度级别高,焊接施工难度大。是常见易开裂的焊接件。
3 焊接件常见裂纹与开裂的特点
3.1氢致裂纹 这是一种最常见的冷裂纹。它往往不是焊后立即出现,而有一段孕育期,延迟一段时间才产生,亦称延迟裂纹。这种延迟现象主要由氢引起,因此又称氢致延迟裂纹,或简称氢致裂纹、氢裂纹。 氢致裂纹开裂部位:对于强度不很高的碳钢与合金结构钢焊接接头,往往先在热影响区粗晶区开裂,扩展到其他区域;强度很高时往往先在焊缝区开裂,扩展到热影响区。 按开裂位置可分为:焊缝金属裂纹、热影响区裂纹; 按相对焊缝的启裂和扩展位置,热影响区氢致裂纹通常有三种形态和部位: ⑴ 焊趾裂纹 一般起源于焊缝趾部(焊缝表面与热影响区交界处)具有明显应力集中的地方,再向热影响区和母材延伸。 ⑵ 焊根裂纹 这是最常见的氢致延迟裂纹,起源于第一层焊道根部与热影响区相交处应力集中****的部位,然后向热影响区和焊缝延伸。究竟向何处延伸,取决于母材和焊缝的强度,塑性、和根部的形状。 ⑶ 焊道下裂纹 发生于焊道下方离熔合线不远的粗晶区内,其走向大体于熔合线平行。是一种微小裂纹,往往不能在焊件表面发现,它不是一条连续裂纹,而是由一条条小的显微裂纹集合而成。这种裂纹往往在使用含氢量较高的焊条、小线能量电弧焊接高强钢时现。 引起氢致开裂的原因:硬化组织、应力、和扩散氢,其中扩散氢为主导因素。 3.2 淬硬裂纹 由淬硬组织引起。某些钢种淬硬倾向很大,焊后冷却过程中,由于相变产生很脆的马氏体,在焊接应力的作用下引起开裂。这种开裂与氢的关系不大,没有氢的作用也会开裂。 例如:弹簧钢、Mn13耐磨钢、某些高强钢以及异种钢焊接时,都可能出现这种裂纹。它的产生既然不取决于氢的存在,也就没有裂缝延迟出现的特征,在焊后可以立即发现。 3.3焊缝表面缺陷引起的裂纹 由于施工操作不当造成的焊接缺陷,也是产生焊接裂纹的重要因素。主要有:焊缝表面形状不符合技术要求。如余高过大、咬边、弧坑、熔合不良等缺陷。 焊缝表面缺陷一般具有明显应力集中、形成裂纹源,或焊缝截面尺寸减小, 承载强度降低,造成焊接开裂。 3.4 疲劳裂纹 疲劳是由于在重复载荷的作用下,导致焊接接头或材料产生裂纹,开裂、扩展、失效的一个过程。工作应力往往远远低于材料的屈服强度。钢材的强度越高,缺口效应引起的应力集中程度对钢材疲劳强度的敏感性就越大。 3.5施工不当,焊缝存在熔合不良、未焊透、咬边等缺陷,造成焊缝金属有效厚度不足,承载强度降低,形成裂纹。
4 焊接开裂修复 焊接开裂修复是工程机械施工过程中设备维修常见的手段,由于受施工现场加工设备、材料、工具、工人技能水平等条件的限制。一定程度上会给正确、有效的焊接修复带来影响。因此,了解与掌握合理、可行的焊接修复技术,很有必要。 4.1实物焊接开裂分析 实物焊接开裂分析是根据开裂的形态、位置分析导致焊接开裂的原因。目的是为了正确制定焊接修复方案和焊接修复工艺方法提供依据,防止焊接开裂再次产生,力求修复后焊接件满足设备正常作业,保障施工。实物焊接开裂分析主要从以下几方面进行。 4.1.1开裂状态分析: 观察开裂出现在焊接件的位置与形态。开裂的位置是在焊缝上还是在母材上,测量开裂长度尺寸、扩展方向、断口特征;开裂部位的焊接件变形状况,分析焊接件开裂与工作载荷的关联因素。初步确定焊接开裂是由焊接缺陷引起还是设备作业过载引起。 4.1.2化学成分分析: 化学成分分析是判定母材焊接工艺性(可焊性)、进行焊接工艺评定与制定焊接修复工艺的重要依据。通过母材的化学成分计算碳当量判定母材的可焊性。 ⑴ 工程机械焊接件常用钢材碳当量与可焊性参见表四。
 表四 ⑵ 有条件时对缺陷部位的母材用手电钻打孔,取铁屑样进行母材的C、Si、Mn、P、S、Cr、Mo、Ni、V、Cu等化学成分进行检验,确定母材的化学成分含量、再查阅相关金属材料手册等技术资料判定母材牌号、强度级别,通过计算母材的碳当量判定母材可焊性。 4.1.3焊接件结构特征分析 焊接件用钢板厚度尺寸较大时,刚性较强,因而焊缝拘束度较大。焊缝在冷却过程中的收缩变形大量存在于焊缝金属中,容易产生较大应力,引起焊缝裂纹,因此在焊接修复时要采取相应对策。 4.2 焊接修复方案与修复工艺制定 4.2.1焊接修复方案制定主要是根据焊接件开裂的程度、焊缝形式及维修场地具备的焊接设备、焊接材料、焊工等条件制定可行的修复施工方法。 4.2.2修复工艺制定内容 ⑴ 焊接方法:焊接修复一般选择焊条电弧焊或气体保护焊。包括采用焊接材料、焊接设备、预热等内容。 焊接材料的选择。焊接方法首先是焊材的选择,焊材选择原则是依据母材的强度要求来确定。工程机械重要焊接件较多采用屈服强度为275-345Mpa的钢材如Q345(16Mn),一般采用等强匹配原则。 随着工程机械焊接结构趋向于高参数、大型化、耐磨、重载、轻量化的方向发展,采用了低合金调质高强钢。在此类钢材强度级别较高时,焊材选择以保证焊接接头的塑韧性的原则可采用低强匹配。 焊接设备选择。焊接设备选择根据选择的焊材种类、修复场所具备的条件确定选用交、直流弧焊电源。 预热。预热主要根据母材的焊接性较差、板材厚度尺寸大、低温环境施工等来确定。以保证焊接接头性能,提高焊接接头抗裂性。 当母材的碳当量≥0.45、板材厚度尺寸≥80mm、环境温度≤5℃进行预热。 一般焊材选择参见表五。
 表五 ⑵ 焊缝坡口形式设计 坡口制备是保证焊缝良好熔合与熔透性的关键工序,根据开裂部位确定焊缝坡口形式是修复工艺的重要内容。坡口形式根据焊缝形式与板厚尺寸确定。 一般板厚≤4mm,对接焊缝可不制备坡口,在板厚≥5mm为保证焊缝熔透性,要制备坡口,由于焊接修复施工容易受到坡口加工、焊接位置等条件的限制,一般采用单面焊。较多采用单面V形坡口或V形坡口形式。 ⑶ 焊接工艺规范制定 焊接修复工艺规范内容主要有焊材牌号、焊材规格、焊接电流、电弧电压 保护气体种类流量、焊接速度、预热温度等。 选择工艺规范时要考虑焊接接头的性能。尤其是碳当量较高的母材焊接接头热影响区对焊接规范要求严格。焊接修复前,应进行工艺评定或工艺试验确定合理的工艺参数。 4.3焊接修复施工及要求 4.3.1工件清理 焊接修复前,将焊接件开裂部位周围粘附的泥土、油污、水、锈蚀、油漆等污物彻底清理干净,露出金属光泽。 4.3.2矫形 焊接件往往在开裂部位通常产生不同程度的变形,在焊接修复前对变形部位进行矫正,焊接变形矫正采用加热矫正、机械施力矫正及两种方法结合运用。 采用火焰加热矫正方法,加热温度在600-800℃,同一加热位置加热次数不应超过两次。焊件热状态矫正,一般不得在蓝脆温度(250-500℃)进行,冷状态矫正不得在环境温度低于-12℃进行。 4.3.3焊前准备 检查焊条、焊丝牌号、规格与焊接用气体、电焊机型号是否符合工艺要求。 焊条按要求进行烘干与保温,一般酸性焊条根据受潮情况在75-150℃烘干1-2小时;低氢型焊条烘干温度在350-380℃,保温时间1.5-2小时,烘干后应缓冷放置于110-120℃的保温箱中存放、待用。 实心焊丝应无油污、锈蚀、镀铜层应完好无损。操作者对焊接机械设备、工具、吊具、防护用品及工位场地进行自检,确认符合安全操作规程。 4.3.4缺陷清除与坡口制备 ⑴焊接件缺陷为裂纹时,根据检测确定的缺陷位置、长度尺寸、深度尺寸,用火焰切割方法、凿除、砂轮打磨等方法清除缺陷。 清除裂纹前应在裂纹两端打止裂孔并清除裂纹及其裂纹两端30-50mm长度的焊缝或母材。应将刨槽加工成四侧边斜面角大于15°的坡口或按工艺要求制备坡口。 ⑵焊接件缺陷为裂断或断开时,分别对断口进行清理、进行坡口加工。 采用氧-乙炔火焰切割后,必须将坡口面切割熔渣与氧化物用砂轮打磨清理干净,露出金属光泽。 4.3.5装配焊接 坡口装配间隙应符合工艺的规定,一般对接坡口间隙为1~3mm,角焊缝坡口装配间隙为0~2mm。 定位焊缝的长度为焊接接头中较薄板厚度的4-5倍,间距不得超过300mm,定位焊缝的高度不得超过正式焊缝的2/3,****不超过6mm。定位焊应布置在焊缝交叉口的50mm以外,定位焊缝的起弧与收弧应平滑过渡。定位焊焊缝不得有裂纹,否则必须清除重焊,定位焊焊缝如存在气孔、夹渣应清除。 焊前预热用大号气焊焊矩、割枪、电加热板或专用喷枪、火焰加热器加热;采用红外测温仪测温。预热时的加热区域应在焊接坡口两侧,宽度为各焊件施焊处厚度2倍以上,且不小于100 mm。预热温度一般在100-150℃。 焊接要求焊接施工应在装配-定位焊检验合格后尽快进行。低合金高强钢、合金钢或焊件厚度超过300mm,应在引弧板或坡口内引弧,禁止在非焊接部位引弧,也不得在焊缝端部引弧。 在未作预热要求的情况下,焊接环境气温低于10℃或相对湿度大于85%,应将焊缝区加热到20℃以后再焊接。 多层焊接时,施焊过程中控制层间温度不超过规定的范围。焊接预热时,应控制层间温度不得低于预热温度。碱性焊条施焊时,应采用短弧焊。 4.3.6焊接检查 所有焊缝外形均匀、成形良好。焊道与焊道、焊道与基本金属间过渡平滑,焊渣与飞溅清除干净。角焊缝焊道与基本金属平缓过渡。所有焊缝均不得存有裂纹、烧穿、熔合不良等缺陷。
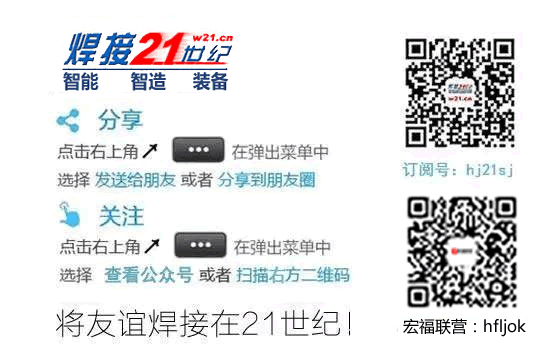 |